

- DC MOTOR CONTROL WITH HIP4082 DRIVER
- DC MOTOR CONTROL WITH HIP4082 PLUS
- DC MOTOR CONTROL WITH HIP4082 FREE
The low thermal resistance and low package cost of the TO-220 contribute to its wide acceptance throughout the industry.” The TO-220 package is universally preferred for all commercial-industrial applications at power dissipation levels to approximately 50 watts. This benefit, combined with the fast switching speed and ruggedized device design that HEXFET power MOSFETs are well known for, provides the designer with an extremely efficient and reliable device for use in a wide variety of applications. According to the IRF3205 datasheet: ”Advanced HEXFET? Power MOSFETs from International Rectifier utilize advanced processing techniques to achieve extremely low on-resistance per silicon area. This MOSFET offers nice characteristics that are essential for this application, very low RDSon resistance, and high current handling capability. I’ve selected 4 IR3205 to do the switching.
DC MOTOR CONTROL WITH HIP4082 DRIVER
Schematic diagram of the H-Bridge DC motor driver As it is clear, the heart of the circuit is two IR2104 MOSFET driver chips. Theoretically, the above-mentioned MOSFET can handle currents up to 80A, however, in practice we can expect to get currents up to 40A if the MOSFET temp[erature is kept as low as possible, using a big heatsink or even a fan.įigure 1 shows the schematic diagram of the H-Bridge DC motor driver. In this article/video, I have introduced a complete H-Bridge DC motor driver using four IR3205 power MOSFETs and two IR2104 MOSFET drivers. The main advantages of using an H-Bridge driver are: high efficiency, rotation direction change, and braking the motor. Moisture Sensitive Surface Mount Devices (SMDs)Ĩ0V, 1.25A Peak Current H-Bridge FET DriverĨ0V, 1.25A Peak Current H-Bridge 80V, 1.25A Peak Current H-BridgeĨ0V/1.25A Peak, Medium Frequency, Low Cost, Half-Bridge DriverĨ0V, 500mA, 3-Phase MOSFET Driver 1.An H-Bridge (Full-Bridge) driver is quite popular in driving loads such as brushed DC motors and it is widely used in robotics and industry. TB363, Guidelines for Handling and Processing
DC MOTOR CONTROL WITH HIP4082 PLUS
DC MOTOR CONTROL WITH HIP4082 FREE
Drives 1000pF Load in Free Air at 50☌ with Rise and Fall.Independently Drives 4 N-Channel FET in Half Bridge or.For applications needing higher drive capability the HIP4080A and HIP4081A are recommended. This set of features and specifications is optimized for applications where size and cost are important. The HIP4082 does not contain an internal charge pump, but does incorporate non-latching level-shift translation control of the upper drive circuits. The HIP4082’s reduced drive current allows smaller packaging and it has a much wider range of programmable dead times (0.1 to 4.5µs) making it ideal for switching frequencies up to 200kHz.
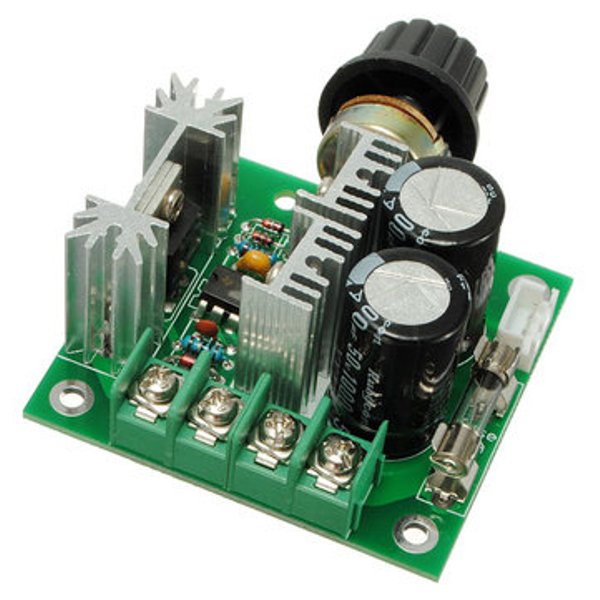
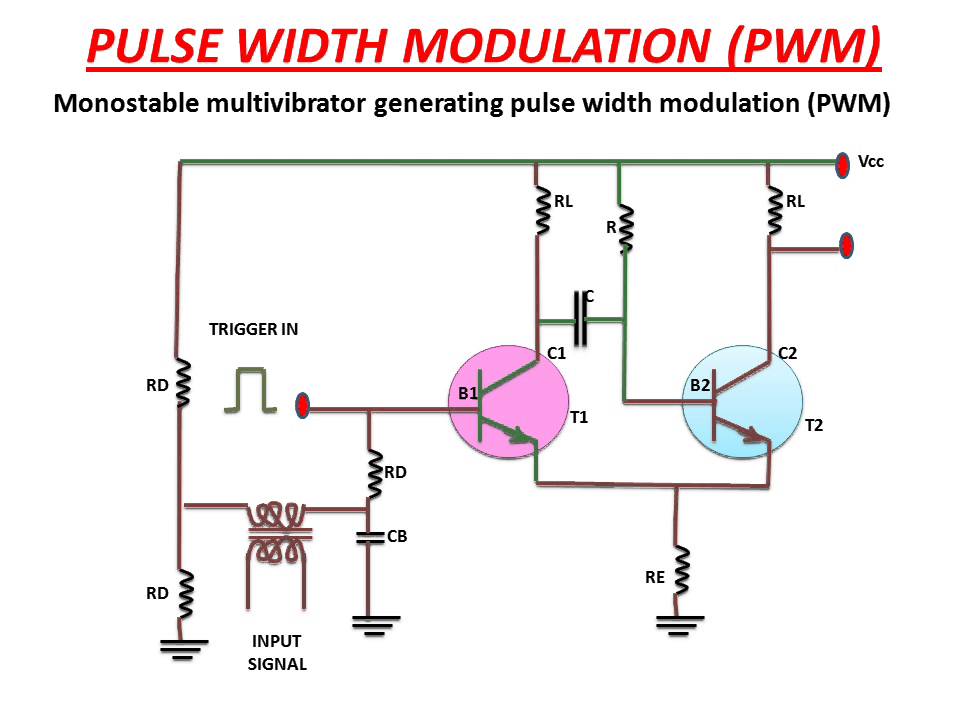
Similar to the HIP4081, it has a flexible input protocol for driving every possible switch combination except those which would cause a shoot-through condition. With operation up to 80V, the device is best suited to applications of moderate power levels. Specifically targeted for PWM motor control and UPS applications, bridge based designs are made simple and flexible with the HIP4082 H-bridge driver.

The HIP4082 is a medium frequency, medium voltage H-Bridge N-Channel MOSFET driver IC, available in 16 lead plastic SOIC (N) and DIP packages.
